What Does FIFO Stand for in Inventory Management?
In the world of wholesale and e-commerce fulfilment, inventory management is more than a back-end operation; it’s a key driver of profitability and operational efficiency. Among the many methods used to track and control stock, the FIFO method remains one of the most trusted and widely adopted approaches across industries.
But what does FIFO stand for? How does it work in practice? And why is it essential for businesses managing large product volumes or fast-moving consumer goods?
In this comprehensive guide, we explore everything you need to know about FIFO in inventory management, from its definition and benefits to practical implementation strategies and common mistakes to avoid.
What Does FIFO Stand For?
FIFO is an acronym for First In, First Out. In inventory management, this means that the first items added to your stock (first in) are the first to be sold or used (first out).
This system ensures that inventory is rotated properly, so older stock is used or sold before newer arrivals. It minimises the risk of obsolescence, spoilage, or depreciation and is especially important for businesses that sell perishable or time-sensitive goods. Sectors like food and beverage, cosmetics, pharmaceuticals, fashion, and electronics often rely heavily on FIFO to maintain product quality, meet regulatory standards, and manage costs effectively.
FIFO also supports accurate cost accounting. When stock prices fluctuate, using older inventory costs for sales figures helps reflect real-time profitability. This matters especially during periods of inflation, as older (cheaper) inventory is sold first, potentially boosting reported profits.
FIFO in Simple Terms:
Imagine stacking tins of soup on a shelf. Under the FIFO method, the tin you placed on the shelf first (the oldest) is the one you sell first. If you always take the front tin (first in) and sell it first (first out), that’s FIFO. If you were to ignore FIFO and sell the newer tins behind the older ones, you’d eventually be left with expired or outdated products.
FIFO helps avoid that scenario, and in large-scale operations, it supports warehouse efficiency, reduces product losses, and improves customer satisfaction.
![FIFO method example in inventory management with older stock placed for first dispatch]](https://cdn.prod.website-files.com/678f822323cac45b996ceb1e/686ec735ad318df5e9a48bd1_pexels-tiger-lily-4481326.jpg)
Why FIFO is Important in Inventory Management
The FIFO method plays a central role in how inventory is controlled, valued, and utilised. For businesses, especially those in wholesale, e-commerce, and retail, implementing FIFO delivers measurable benefits across multiple operational and financial dimensions:
1. Cash flow and profitability
FIFO allows businesses to sell older, lower-cost stock first, especially in times of inflation. This can reduce the reported cost of goods sold (COGS), which in turn increases gross profit margins. Better profit margins improve overall financial health, giving businesses more flexibility in reinvestment, staffing, and scaling operations.
2. Cost of Goods Sold (COGS)
With FIFO, COGS reflects the cost of the oldest inventory. This matches the actual physical flow of products and delivers more accurate and consistent financial reporting. For accounting and tax purposes, having clarity in COGS improves budget forecasting, pricing strategies, and audit readiness.
3. Warehouse efficiency
Implementing FIFO helps streamline warehouse operations. It encourages an organised system where older inventory is placed at the front and newer stock at the back. This minimises time spent searching for items and reduces the chances of human error in order picking, which is crucial for high-volume e-commerce fulfilment operations.
4. Product quality control
FIFO supports high product quality by ensuring that older stock is dispatched first. This is particularly vital in sectors like food, pharmaceuticals, and cosmetics, where expiry dates and product freshness impact brand trust and compliance. With FIFO, products are less likely to remain unsold due to ageing or degradation.
5. Compliance with accounting standards
FIFO is widely accepted under IFRS (International Financial Reporting Standards) and UK GAAP (Generally Accepted Accounting Principles). It offers a transparent, standardised approach to inventory valuation, which simplifies regulatory compliance, financial audits, and reporting to stakeholders.
By prioritising FIFO in inventory management, businesses gain control over their supply chain, reduce waste, and maintain high levels of customer satisfaction. When implemented within a broader strategy such as working with a wholesale 3PL provider or offering e-commerce fulfilment services, FIFO becomes an operational asset that drives long-term efficiency and growth.
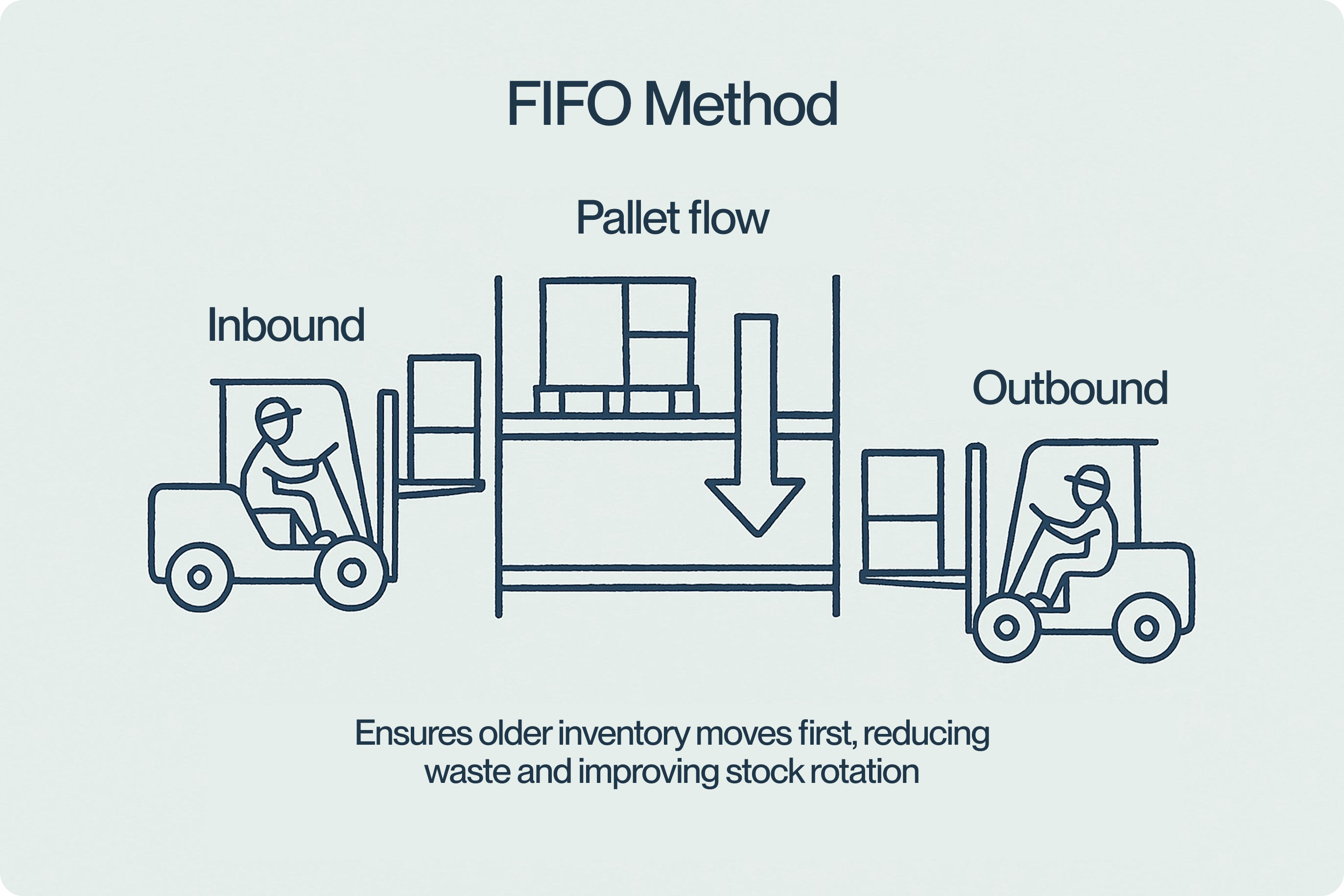
How the FIFO Method Works in Practice
Under FIFO, your inventory management system or warehouse team will always move the oldest stock first. This can be done manually in smaller operations or via automated processes in advanced warehouse setups.
Let’s consider a FIFO method example:
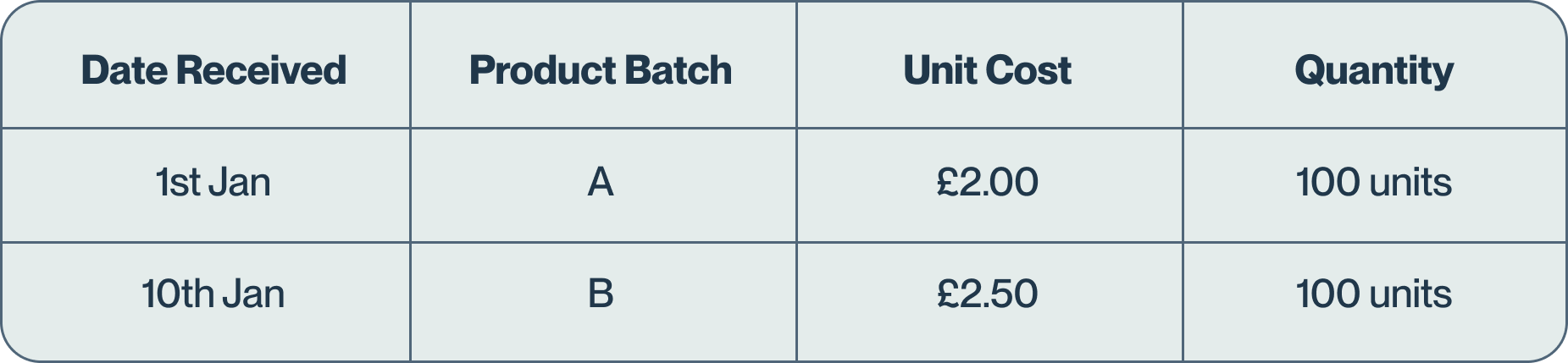
On 15th January, 100 units were sold. According to FIFO, these 100 units came from Batch A (1st Jan) at £2.00 per unit.
COGS = 100 units × £2.00 = £200
Remaining Inventory: 100 units from Batch B at £2.50
This approach provides a clear method of cost calculation and aligns your stock turnover with real-world consumption.
Benefits of Using the FIFO Method
Adopting the FIFO inventory method offers a wide range of operational and financial benefits for businesses that manage stock regularly, particularly those involved in wholesale, retail, or e-commerce fulfilment operations. Below is a closer look at the key advantages, with detailed explanations for each:
1. More Accurate Stock Valuation
FIFO provides a more transparent and realistic reflection of your stock’s actual cost by aligning product usage with the order in which items enter the inventory. When older inventory is sold first, your valuation closely mirrors the true cost of inventory on hand. This prevents inflated valuations due to older, cheaper stock being left unused, which could distort financial statements or lead to inaccurate forecasting.
2. Improved Profit Margins in Inflationary Periods
In times of rising costs, the FIFO method can enhance reported profitability. By using the lower costs of older inventory for calculating the cost of goods sold (COGS), businesses can report higher gross margins. For example, if inventory prices are rising, selling items purchased at lower prices (older stock) means your profit margins widen, even if your selling price remains constant.
3. Better Product Quality and Customer Satisfaction
FIFO ensures older products are dispatched before newer ones, which is vital for goods with expiration dates or quality degradation over time. This significantly reduces the chances of delivering expired, stale, or out-of-date products to customers. In sectors like health and beauty, FMCG, electronics, and fashion, maintaining product integrity is critical to preserving brand reputation and avoiding costly returns or complaints.
4. Simplified Financial Reporting and Compliance
FIFO is recognised by major accounting frameworks such as UK GAAP and IFRS, making it easier to align internal records with external financial statements. Because inventory turnover matches the natural product flow, audits become less complex, inventory write-downs are minimised, and reconciliation is more straightforward at the end of each financial year.
5. Enhanced Warehouse Efficiency
Following FIFO naturally supports structured inventory placement in the warehouse—commonly referred to as “first-through” layouts. This leads to more predictable pick paths, reduces time spent locating products, and helps warehouse staff avoid mispicks. It also enables the use of automated systems or barcoding strategies that reinforce FIFO logic.
6. Lower Waste and Shrinkage
Businesses that do not implement FIFO often accumulate outdated or unsellable stock, leading to higher shrinkage and disposal costs. With FIFO, stock is continually rotated and sold in a timely manner, reducing the risk of obsolescence. This contributes to more sustainable business operations and supports waste reduction goals.
7. Real-Time Decision-Making and Forecast Accuracy
With FIFO, businesses benefit from real-time data on how fast older stock is moving, helping managers make better decisions about reordering, seasonal promotions, or inventory clearance. This visibility can enhance demand planning and optimise cash flow management.
8. Builds Trust in Fulfilment Partnerships
For any trusted fulfilment company, adhering to FIFO principles reassures clients that their stock will be handled responsibly and dispatched with product freshness in mind. It demonstrates operational discipline, reduces the risk of service errors, and builds long-term client relationships, especially in high-volume e-commerce or wholesale 3PL provider partnerships.
FIFO vs LIFO: Key Differences
FIFO is often compared with LIFO (Last In, First Out), another inventory method where the newest items are sold first. Here’s how they differ:
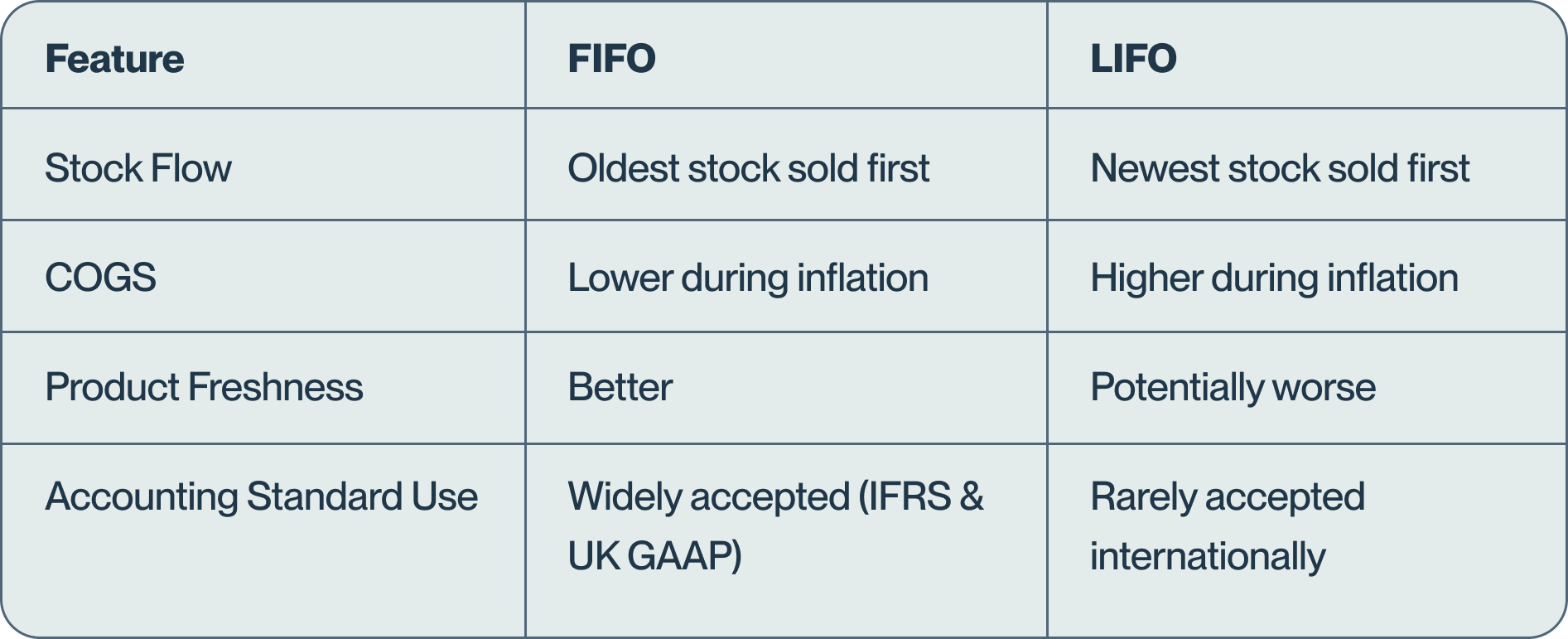
FIFO in Wholesale Operations
For wholesalers, particularly those handling fast-moving consumer goods (FMCG), electronics, or seasonal products, implementing FIFO is essential, not just beneficial. In such high-volume environments, mismanaging inventory can result in overstocking, expired products, and lost profits. FIFO ensures older inventory is cleared first, freeing up warehouse space, maintaining product quality, and supporting reliable stock turnover.
Effective FIFO implementation in wholesale environments typically includes:
- Clearly labelled batch tracking: Each product batch is tagged with receipt dates, making it easier for pickers to identify the oldest stock.
- Zoned shelving by arrival date: Inventory is stored in designated FIFO zones that guide pickers naturally toward older stock.
- Barcode scanning for verification: Scanners confirm the batch and expiration sequence to enforce FIFO rules and avoid mispicks.
Wholesale operations often rely on automation to manage these elements, particularly when partnered with a wholesale 3PL provider. These fulfilment centres use advanced warehouse management systems (WMS) and process flows designed to support fast, accurate FIFO execution at scale.
FIFO in E-commerce Fulfilment Services
In the e-commerce space, where competition is fierce and customer expectations are high, FIFO plays a critical role in delivering products in excellent condition. Items like skincare, supplements, tech accessories, and fashion goods often have shelf-life concerns or are trend-sensitive. Using FIFO ensures these products are dispatched in the right sequence, preserving quality and reducing returns.
When e-commerce brands partner with 3PLs that offer professional e-commerce fulfilment services, they benefit from:
- Trained teams that understand FIFO procedures and ensure proper handling.
- Smart software that flags and prioritises older SKUs for picking.
- Warehouse layouts that physically support FIFO flow, with front-facing older stock and backfilling for new arrivals.
This system helps maintain customer trust, improve delivery experiences, and reduce revenue losses due to expired or unsellable inventory. Moreover, it supports sustainability goals by reducing waste and minimising the environmental impact of returns and disposals.
FIFO Automation and Software Tools
Modern inventory management has evolved with technology, making FIFO more efficient and less prone to human error. Today’s best-in-class inventory platforms include built-in FIFO functionalities, allowing businesses to automate key processes and reduce manual oversight.
Key capabilities include:
- Real-time tracking of batch arrivals – Inventory systems log each batch upon arrival and update stock positions in real time.
- Automated stock picking rules – FIFO algorithms can be embedded in order fulfilment processes, prioritising older inventory for picking.
- Barcode or RFID scanning – Scanners validate each pick against the expected batch, ensuring that staff follow FIFO logic.
Popular platforms like NetSuite, Oracle NetSuite WMS, Linnworks, and bespoke 3PL fulfilment software allow for full FIFO customisation and reporting. For example, a beauty brand managing products with 6-month shelf lives can configure alerts when stock reaches 75% of its expiry period, triggering prioritised clearance or promotional strategies.
This level of automation not only improves compliance and stock accuracy but also gives decision-makers critical insights into ageing inventory and turnover trends.
Real-World FIFO Method Example
Let’s take a hypothetical business selling organic protein bars:
- January: Received 2,000 bars, cost per unit £1.00
- February: Received 2,000 bars, cost per unit £1.10
- March: Sold 3,000 bars
Using FIFO, the cost of goods sold (COGS) is:
- 2,000 x £1.00 = £2,000
- 1,000 x £1.10 = £1,100
- Total COGS = £3,100
Accurate reporting supports better pricing decisions, margin forecasting, and tax compliance.
FIFO naturally supports sustainability by reducing waste, preventing expired stock, and minimising the need for emergency restocking or disposal. In a world where eco-conscious operations are no longer optional but expected, FIFO aligns inventory flow with environmentally responsible practices.
When FIFO is integrated with broader sustainability measures, its impact is amplified:
- Compostable or recyclable packaging: Older stock can be packed with environmentally friendly materials, ensuring a lower carbon footprint per shipment.
- Eco-friendly dunnage: Using paper void-fill, biodegradable air pillows, or recycled cardboard adds a green layer to FIFO-focused packaging operations.
- Carbon-reduced delivery routes: FIFO helps streamline warehouse operations, reducing unnecessary stock movement and enabling route optimisation for lower emissions.
Many businesses are now incorporating Environmental, Social, and Governance (ESG) goals directly into their FIFO Standard Operating Procedures (SOPs). For sectors like food, healthcare, and cosmetics, where product life cycles are closely monitored—this approach ensures full regulatory compliance and positions brands as sustainability leaders.
Advanced reporting tools can also track sustainability KPIs in FIFO systems, such as stock ageing, shrinkage reduction, and packaging lifecycle metrics. With consumers increasingly valuing responsible business practices, leveraging FIFO as part of a broader eco-strategy provides both commercial and reputational advantages.
Final Thoughts and Getting in Touch
FIFO is more than a method, it’s a mindset. Whether you operate a fast-paced warehouse or run an online store, applying FIFO ensures your inventory moves efficiently, your finances stay accurate, and your customers stay satisfied.
At Airbox Fulfilment, we help you streamline operations and improve profitability through proven FIFO practices.
We’re your trusted fulfilment company whether you’re seeking integrated inventory control, end-to-end dispatch support, or a scalable wholesale 3PL provider.
Need help improving your FIFO compliance or planning your next stock rotation cycle?
Contact our team or reach us directly at:
Let’s optimise your stock today, and scale smarter tomorrow.